Key Principles of Industry 4.0
The concept of Industry 4.0 was first proposed at the Hannover Fair in 2011. Klaus Schwab who was founder and chair of the World Economic Forum (WEF) wrote that into a book, The Fourth Industrial Revolution, in 2016. In the book, he described how some of the technologies have reached critical mass in development and adoption. And how this can permanently transform business models and the world’s economy.
In his book, Schwab mentioned several technologies that are enabling IR 4.0. Other global organisations have added a few more. These technologies are experiencing explosive growth because they can now be accessed easily and cheaply due to the plentiful supply of devices, computing and storage connected by ubiquitous communications networks. Figure 1 shows the global pillars of IR 4.0 and the reasons IR 4.0 can happen now.
Fig 1: Why can IR 4.0 happen now but not earlier?
The IR 4.0 Enterprise and Factory
Figure 2 shows the IR 4.0 Enterprise and Factory. Traditionally, there are 2 distinct networks: the Information Technology (IT) network, which is used for administration (emails, Finance, HR), reporting, analytics; and the Operational Technology (OT) network which is used to run the factory in real-time. They were built and managed differently because the networking technologies could not cater to conflicting demands.
Fig 2: 5G features in an IR 4.0 factory
We can see in a simplified factory with a mix of network feature demands. Management of robots, AGVs and conveyor lines needs a dedicated network with real-time response. There may be a low-speed network that collects data from sensors for warehouse humidity, machinery noise levels and factory floor temperatures. There may be another high-capacity network that connects quality control cameras, factory and office compound surveillance cameras, and training simulation systems to application servers and storage on-site or in the Cloud.
To monitor and control delivery trucks on the roads, the IR 4.0 Enterprise will need to resort to a public mobile network such as 4G or LTE as today’s private networks are very local.
All these devices and networks send data back to the Operation and Management Centres for analytics and reporting, also for machine learning, pattern and trend recognition.
Having so many networks with different technologies and topologies is difficult and expensive to manage and operate. The corporate technology office is always looking to streamline and integrate the IT and OT networks.
What is the role of 5G in IR 4.0?
5G is the first time that a single mobile network can cater for different and seemingly opposing requirements: large data volume vs many devices vs low latency. 5G has a feature called Network Slicing. This virtualises the 5G network so that applications and devices on a particular slice, can treat that as its own private network. Each application can make on-demand request of a slice type to the 5G network. 5G network is Cloud-native so it can scale automatically.
Remember in the previous installment of our 5G series where we showed Figure 3? So, each of those usage scenarios can represent a 5G network slice type in our factory. You can see how eMBB, uRLLC and mMTC map into the respective coloured boxes of the production floor in Figure 2.
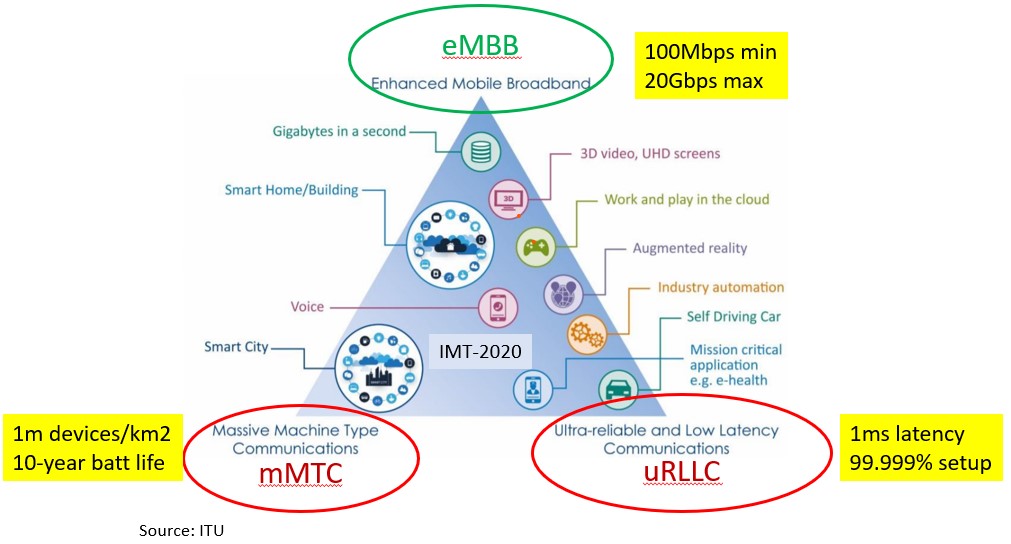
ITU IMT-2020 5G key use cases mMTC uRLLC eMBB
Figure 3 5G Usage Scenarios
As 5G is Cloud-native. It can scale up and down quickly should the factory build a new production line or phase out old ones, or roll out higher resolution images for quality inspection, or deploy more sensors and cameras for safety compliance or environment surveillance, or when there are changes in truck volumes coming in and out for shipment and deliveries.
5G also brings inherent end-to-end Quality-of-Service (QoS) and security that other wireless networks cannot cater to.
Multi-access Edge Computing (MEC) has been included as part of 5G standards, allowing the factory to push latency-sensitive processing to the cloud edge.
5G is suitable for both the IT and OT operating scenarios so it fits nicely in the middle of the IR4.0 manufacturing environment as seen in Figure 4.
Here is a video of how 5G is used in Industry 4.0 in a metal stamping factory in Spain.
If you would like to know more, we have this use case as a case study in this course.
Fig 4 5G in a Full IR4.0 Manufacturing Environment
New Skills Are Needed
As with all transformations, IR 4.0 is not just a play of the technologies listed in Fig 1. We need Process and People upgrades too. Besides the major technology pillars, we will need skills in AGILE and DevOps methodology, Rapid Prototyping, Supply chain management and manufacturing process optimisation. It is not just skills but skill set upgrades and mindset changes. Below shows a sample matrix of skills for 5G in developing an IR4.0 product context.
Where can I pick up such skills?
If you want to know more about how IR 4.0 and other applications make use of 5G mobile networks, please click on the links below.
CS1777 Using 5G in IOT End-to-end Application Design, with Business Cases
CS1337 5G for Management – An Application Perspective
CS2030 5G in Smart City Applications
CS1063 Overview of 5G Technology
There are also many courses that DreamCatcher has on other IR 4.0 requisite technologies such as AI, IOT, Cloud Computing, Data Analytics.
Great summary of why IR4.0 and 5G